Uma visão geral sobre a aplicação da técnica
de Análise de Risco FMEA
Paulo Rogers Helrighel
Especialista em Gestão de Projetos pela FAE Business School, Especialista em Engenharia de Campo Qualidade Óleo & Gás (PUC/PR), Especialista em Engenharia de Segurança do Trabalho pela Universidade Tecnológica Federal do Paraná (UTFPR). Cursando o MBA de Riscos da Brasiliano INTERISK
De acordo com Puente (2001) e Helrighel (2009, p.67) em 1963 a NASA começou a desenvolver uma técnica específica para identificar sistematicamente as falhas potenciais de projeto por ocasião do Programa Apollo. Superada a fase áurea das missões espaciais, a ferramenta ressurge sob a denominação de “FMEA”, sigla em inglês para “Análise de Modos e Efeitos de Falha”
A partir de 1977, a Ford aplicou a ferramenta na melhoria do processo de fabricação de seus produtos. É um marco importante, pois modifica o contexto no qual o método passou a ser empregado: o projeto constituído de atividades não repetitivas dá lugar ao processo integrado por etapas de fabricação cíclicas e repetitivas (GILCHRIST, 1993 apud HELRIGHEL, 2009, p.67).
A aplicação de FMEA foi largamente empregada na década de 1990 nas mais variadas disciplinas de engenharia, as quais adotaram as ferramentas de gestão da qualidade popularizadas na implementação do Controle de Qualidade Total ou “TQC” (CAMPOS, 1992 apud HELRIGHEL et al., 2007, p.130).
O ciclo de desenvolvimento de engenharia iniciava na concepção e avançava para as subsequentes fases de projeto, processo e manufatura. Este conceito só sofreria alteração com o advento da engenharia simultânea, ou “engenharia concorrente” conforme denominada por Cleland (2003, pp.79-82), a qual foi uma das predecessoras do moderno gerenciamento de projetos.
Conforme o Automotive Industry Action Group (2008, p.137), a “Análise de Modos, Efeitos e Criticidade”, FMECA, é frequentemente utilizada como sinônimo de FMEA dada a similiaridade entre as técnicas. A diferença é o conceito de criticidade que inclui meios de classificar os modos de falha pela severidade e assim, priorizar contramedidas. Isso é feito combinando a medida de severidade e frequência de ocorrência para produzir o índice de criticidade (INTERNATIONAL ELECTROTECHNICAL COMMISSION, 2006, p.14).
Aplicação da técnica FMEA
De acordo com Helrighel (2007, pp.123-133) há inúmeras técnicas e ferramentas de gestão da qualidade cujo o emprego em larga escala remete aos anos 1990, como o diagrama de causa e efeito (Ishikawa ou espinha de peixe), histogramas, diagrama de pareto, brainstorming, gráficos de controle, etc. Mas, comparada a essas, a técnica FMEA nunca foi uma ferramenta de aplicação simples e seus resultados podem ser comprometidos se alguns pré-requisitos não forem atendidos, como delimitar bem o escopo, trabalhar com equipes multidisciplinares, seguir uma metodologia corretamente aplicada, etc.
Segundo a Associação Brasileira de Normas Técnicas (2012, p.18), FMEA e FMECA são técnicas fortemente aplicáveis em todas as etapas do processo de avaliação de riscos definido pela norma ISO 31000. A própria norma ISO/IEC 31010 tem como objetivo refletir as boas práticas atuais na seleção e aplicação das técnicas de análise de riscos conforme afirma o Brasiliano (2016, p.76).
De acordo com Stamatis (2003) e Helrighel (2009, p.67), a metodologia FMEA procura avaliar de maneira lógica e sistemática o risco de ocorrência de falhas de um processo através de critérios como severidade, modo de ocorrência e modos de detecção. Com base nestes três quesitos: severidade, ocorrência e detecção, a técnica FMEA procedimenta a priorização dos modos de falha em função dos maiores riscos. Em linhas gerais, a metodologia funciona através de etapas distintas.

Principais etapas de execução de FMEA
As principais etapas na execução da ferramenta FMEA, conforme Palady (1997) e Helrighel (2009, p.68) são:
• Listar todas as funções, características ou requisitos do sistema, produto, componente ou processo e para cada uma delas identificar os possíveis modos de falha;
• Identificar os efeitos de cada modo, criando-se um checklist. O qual é tabulado em função da classificação de cada modo em relação à severidade da falha;
• Identificar as causas possíveis para cada modo de falha e a probabilidade de ocorrência. Através de técnicas diversas, levantar as prováveis causas para identificar os meios de prevenção que reduzem a probabilidade de ocorrência da falha;
• No caso de ocorrência do modo de falha, identificar o meio e sua probabilidade de detecção. Onde detecção é a capacidade de identificar a falha após sua ocorrência e antes do cliente ter sido impactado pelo seu efeito final;
• Avaliar o número de prioridade de risco de cada modo de falha e definir as contramedidas para eliminar ou mitigar o fator de risco (STAMATIS, 2003 apud HELRIGHEL, 2009, p.68).
Segundo Palady (1997) e Stamatis, as principais vantagens da utilização da metodologia FMEA são:
• Armazenamento de informações sobre a prevenção de falhas;
• Definição e priorização das ações preventivas (ações recomendadas).
• Identificação das características críticas, redundâncias e procedimentos voltados ao diagnóstico de falhas;
• Melhoria da Qualidade, confiabilidade e segurança de produtos e serviços;
• Redução de tempo, custo de desenvolvimento dos projetos da empresa;
• Priorização das ações do projeto e apoio à análise de novos projetos, programas e portfólios;
A principal razão para a execução da técnica FMEA é a necessidade de melhoria. Para alcançar todos os benefícios, é necessário que o método esteja integrado à cultura da organização (STAMATIS op.cit. apud HELRIGHEL, p.69).
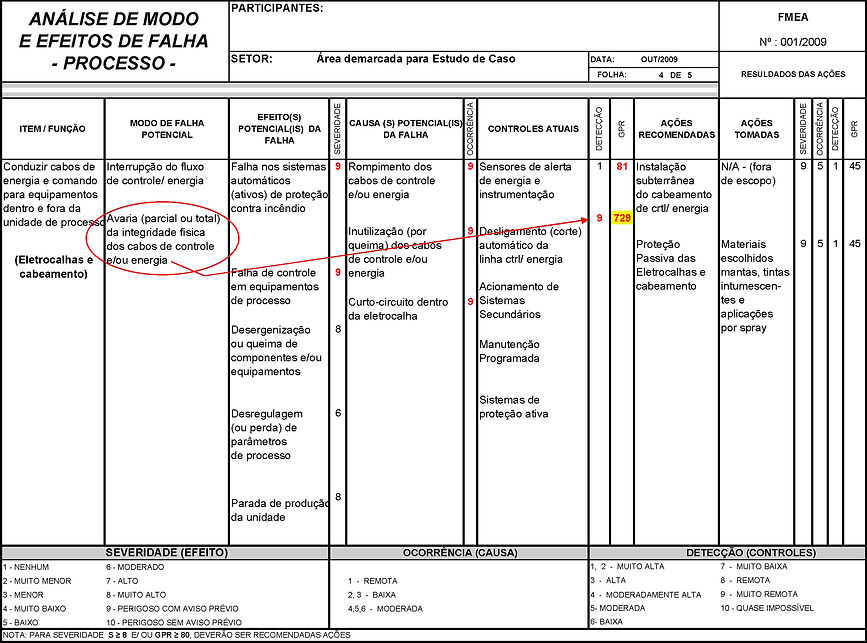
Tipos de FMEA
Stamatis op.cit. apud Helrighel (2009, p.70) menciona dentre os tipos de FMEA:
a) FMEA de Sistema: chamado de FMEA de conceito, é usado para avaliar as falhas em sistemas e subsistemas nos estágios iniciais de definição da conceituação de projeto e precisa ser revisto continuamente durante a vida útil do sistema;
b) FMEA de Produto: é utilizado para avaliar possíveis falhas em produtos antes de sua liberação para fabricação, mas necessita revisão durante a vida útil do produto;
c) FMEA de Processo: é utilizado para avaliar as falhas em processos preliminares à liberação para produção seriada, mas necessita de revisão durante toda a vida útil do processo. Foca as falhas potenciais do processo em relação ao cumprimento dos objetivos para cada uma de suas características e está diretamente ligada à capacidade do processo em cumprir os objetivos definidos para o mesmo;
d) FMEA de Serviço: pode ser empregado de diversas maneiras, uma das quais é a execução de FMEAs específicas na avaliação das etapas do desenvolvimento de um sistema, semelhantemente a um produto. Estas etapas são: sistema de serviço (FMEA de sistema); produto de serviço (FMEA de produto) e processo de execução de serviço (FMEA de processo). Outro modo de executar uma FMEA de serviço é através de uma FMEA que abranja todas as características desde o sistema de serviço até o sistema em si. Para uma aplicação adequada da FMEA é importante formar uma equipe multidisciplinar (STAMATIS op.cit. apud HELRIGHEL, 2009, p.71).

Revisão periódica
Após a sua execução inicial, o método deve ser reempregado como uma ferramenta do cotidiano. A revisão contínua ou periódica é o ponto-chave do processo, pois existem constantes alterações nas condições de um sistema, produto, processo e serviço que alteram o documento de FMEA (HELRIGHEL, 2009, p.69).
Ao ocorrer modificações que possam alterar a gravidade ou impacto da falha no cliente, a severidade deste modo precisa ser revisada sempre que forem incluídas alterações modificando a probabilidade de ocorrência de uma causa e/ou caso surjam informações indicando que a ocorrência é diferente da prevista no documento. Ou ainda, caso existam modificações nos meios de detecção da causa, a referida causa precisa ser revista, assim como novas causas devem ser incluídas quando necessário.
De modo análogo, sempre que ocorram modificações nos meios de detecção de uma determinada falha, a probabilidade de detecção precisa ser revisada.
Essa dificuldade inerente de animação, tornou a FMEA uma aplicação difícil de gerir dentro do contexto de processos tidos como repetitivos e cíclicos. Por experiência, profissionais de chão-de-fábrica declaram a sua preferência por outras ferramentas mais simples e fáceis de gerir através de melhorias contínuas. Pois suas atividades são, em última análise, repetitivas e cíclicas (PALADY op.cit. apud HELRIGHEL, 2009, p.70).
Entretanto, com poucas alterações no macroprocesso, o documento de FMEA, torna-se um “documento vivo” bastante dinâmico e que exige atenção redobrada por parte de seus condutores. Resquícios do contexto da sua criação, pois o método foi criado originalmente para gerenciar riscos de grandes projetos e programas.
Considerações finais
Segundo Helrighel et Higa (2007), os programas de treinamento têm a capacidade de alavancar os esforços de aprimoramento da qualidade do produto. Os fornecedores são estimulados a assimilarem melhorias, proporcionando uma mudança na sua cultura interna. Ou seja, são os treinamentos contínuos que fazem a diferença.
O mesmo pode ser afirmado em relação à revisão contínua da aplicação de FMEA durante toda a vida útil do sistema, principalmente quando ocorrem alterações. Conforme Palady (2009, p.95), isso geralmente acontece com sucesso na implantação simultânea de um processo ou sistema, mas poderá falhar se forem executadas melhorias em determinada parte sem considerar a revisão do processo afetado pelo impacto das respectivas modificações realizadas.
Da mesma forma, Helrighel (p.96) aponta que a desatualização dos dados poderá comprometer a validade de toda a análise de riscos realizada e tornar os resultados incongruentes. Isso pode criar um precedente perigoso para a ocorrência de incidentes e acidentes caso a base de dados esteja há muito tempo defasada ou tenham ocorrido sucessivas alterações que poderiam descaracterizar as análises de risco realizadas e deste modo ter comprometido os resultados obtidos.
Referências
ASSOCIAÇÃO BRASILEIRA DE NORMAS TÉCNICAS. ABNT NBR ISO/IEC 31010. Gestão de riscos - técnicas para o processo de avaliação de riscos. Rio de Janeiro, 2012.
AUTOMOTIVE INDUSTRY ACTION GROUP. Potential failure mode and effects analysis (FMEA): reference manual. USA: 4th edition. 2008.
BRASILIANO, Antônio Celso Ribeiro. Inteligência em Riscos: gestão integrada de riscos corporativos. SP: Sicurezza, 2016, 248p.
CAMPOS, Vicente Falconi. TQC: controle da qualidade total (no estilo japonês). BH: Fundação Christiano Ottoni, Escola de Enhenharia da UFMG, 5ª edição, 1992 (RJ: Bloch Ed.). 229p.
CLELAND, David I.; IRELAND, Lewis R. Gerência de Projetos. RJ: Reichmann & Affonso, 2002. 324p.
GILCHRIST, Warren. Modeling failure modes and effects analysis. International Journal of Quality and Reliability Management, n.982816, 1993.
HELRIGHEL, Paulo Rogers. Proteção passiva contra fogo dentro de uma unidade de destilação atmosférica e à vácuo. Curitiba: UTFPR, Monografia de Especialização em Engenharia de Segurança do Trabalho, 2009. 116p.
HELRIGHEL, Paulo Rogers; HIGA, Daniel Fernandes. Avaliação e seleção de fornecedores no setor automotivo de Curitiba: o caso Cartrom Embalagens S.A. Curitiba: Revista Intersaberes, ano 2, n. 3, pp. 40–57, jan/jun 2007.
HELRIGHEL, Paulo Rogers (organizador) et al. Apostila Grupo de Estudos Gerenciamento de projetos: sumário executivo. Curitiba: Associação de Gerenciamento de Projetos do Paraná, 2007. 191p.
INTERNATIONAL ELECTROTECHNICAL COMMISSION. IEC 60882: Analysis techniques for system reliability – Procedure for failure mode and effects analysis (FMEA). Geneva: 2nd edition, 2006.
PALADY, Paul. FMEA: Análise dos Modos de Falha e Efeitos – prevendo e prevenindo problemas antes que ocorram. SP: Imam, 1997. 270p.
PUENTE, Javier et al. A decision support system for applying failure mode and effects analysis. International Journal of Quality and Reliability Management, v.19 n.2, p.378-397, 2002.
STAMATIS, D.H. Failure Mode and Effect Analysis: FMEA from theory to execution. 2nd edition. Milwaukee: ASQ Quality Press, 2003